Что такое керамическая печатная плата?
Что такое керамическая печатная плата?
Керамическая печатная плата также называется керамической подложкой или керамической печатной платой, керамической медной пластиной, керамической подложкой с медным покрытием, непосредственно соединенной с керамической подложкой из глинозема (Al2O3) или нитрида алюминия (AlN) или другой керамической подложкой (одинарной или двойной) на специальной технологической плате.
Керамическую печатную плату можно описать как органическое связующее и керамический порошок, который проводит тепло. Теплопроводность, при которой изготавливается эта печатная плата, составляет от 9 до 20 Вт/м.
Чтобы пояснить далее, керамические печатные платы - это печатные платы с керамическим материалом в качестве основы. Этот базовый материал обладает высокой теплопроводностью, подобно нитриду алюминия, оксиду алюминия окиси алюминия и оксиду бериллия. Они очень эффективны при передаче тепла от горячих точек и последующем рассеивании этого тепла по всей поверхности.
Помимо этого, изготовление керамических печатных плат осуществляется по технологии LAM. Эта технология представляет собой тип металлизации с быстрой активацией лазером. Таким образом, керамические печатные платы обладают высокой универсальностью и могут легко заменить все традиционные печатные платы целиком. Эта печатная плата позволит достичь этого с еще более высокой производительностью и менее сложной конструкцией.
1. Разница между керамической подложкой и печатной платой
Керамическая подложка - это то, что мы называем керамической печатной платой, керамическая печатная плата и печатная плата имеют одинаковые характеристики межсоединений, проводимости через отверстия. В чем же заключаются различия между керамической подложкой и печатной платой?
(1) Теплопроводность печатной платы и керамической подложки различна.
Керамическая подложка изготовлена из керамической подложки, т.е. среда является керамическим материалом, включая глиноземную керамическую основу, керамическую основу из нитрида алюминия, керамическую основу из нитрида кремния, керамическая теплоотдача очень хороша, теплопроводность керамической подложки от 25 до 230 Вт, теплопроводность различных керамических сред отличается. Теплопроводность керамической подложки из глинозема составляет 25~30 Вт, теплопроводность керамической подложки из нитрида алюминия превышает 170 Вт, а теплопроводность керамической подложки из нитрида кремния составляет 80~90 Вт. В этом случае для изготовления печатных плат обычно используется материал fr4 или металлическая подложка, теплопроводность которой составляет менее 3 Вт, а зазор слишком велик по сравнению с керамической подложкой, особенно в случае необходимости обеспечения высокой теплоотдачи в данной области, керамическая подложка стала очень популярным материалом.
2. Различия между керамической подложкой и изоляцией печатной платы
Керамическая подложка, как правило, слой линии - керамическая основа - структура слоя линии, керамическая подложка изоляции очень хорошо, также определяется керамическим материалом это
(3) Структура тепловыделения керамической подложки отличается от структуры печатной платы
Структура рассеивания тепла керамической подложки представляет собой структуру слоя схемы - керамическое основание - слой печатной платы. Поскольку посередине нет изолирующего слоя, тепло устройства передается непосредственно от керамического основания к слою схемы, и рассеивание тепла происходит быстро, а эффект хороший. печатная плата нуждается в нагреве от среднего слоя - изоляционного слоя - линейного слоя, разделенного изоляционным слоем в то же время, сам диэлектрический слой с низкой теплопроводностью, затем добавьте клей для теплопроводности, эффект теплопроводности все еще не улучшен, часто не удается достичь цели устройство для быстрого отвода тепла. В частности, в некоторых мощных устройствах необходимо использовать керамическую подложку в качестве охлаждающей подложки в области производства, где рассеивание тепла и изменение температуры относительно велики.
(4) Применение керамической подложки и печатной платы отличается
Применение керамической подложки и печатной платы различно, в основном производительность этих двух устройств различна, керамическая подложка используется в областях с высокой теплопроводностью, высоким тепловыделением, высокой изоляцией, таких как светодиодное освещение высокой мощности, модуль высокой мощности, высокочастотная связь, источник питания трека; Обычная печатная плата используется в некоторых более обширных, к тепловыделению, изоляции и другим требованиям не предъявляются строгие требования, используется в частных коммерческих товарах.
(5) Цена керамической подложки отличается от цены печатной платы
Материал и эксплуатационные характеристики керамической подложки и печатной платы различны, и окончательное решение заключается в том, что цены на них разные. Толщина плиты на керамической подложке очень высока, а стоимость производства высока.
Керамическая подложка обладает выдающимися преимуществами, но керамическая подложка хрупкая и имеет высокий процент брака, что требует высокого уровня технологии производства. Однако вы не можете изготовить печатную плату размером более одного метра, как обычные печатные платы. Hitech Circuits имеет более чем 10-летний опыт работы в производстве керамических печатных плат, и многие университеты и научно-исследовательские учреждения сотрудничают с нами, добро пожаловать на запрос.
2.Разница между керамической подложкой и высокочастотной пластиной
Материал другой. Керамическая подложка изготовлена из оксида алюминия или нитрида алюминия, а высокочастотная пластина изготовлена из Rogers, Yaron, PTFE и т.д., с низкой диэлектрической проницаемостью и высокой скоростью передачи данных на частоте.
Производительность отличается. Керамическая подложка широко используется в холодильных установках, модулях высокой мощности, автомобильной электронике и других областях. Высокочастотная плата в основном используется в области высокочастотной связи, авиации, высококачественной бытовой электронике и так далее. Область высокочастотной связи связана с требованиями к рассеиванию тепла, которые обычно необходимо сочетать с керамическим основанием и высокочастотной пластиной, такой как высокочастотная керамическая печатная плата.
1. Нанесение керамической основы
Керамические подложки используются в светодиодных чипах для достижения лучшей теплопроводности. Кроме того, керамическая подложка также используется для изготовления керамических чипов в следующих электронных устройствах:
◆Полупроводниковый модуль высокой мощности
◆Охладитель полупроводника, электронный нагреватель; Схема управления мощностью, схема смешивания мощности
◆Интеллектуальный силовой модуль; Высокочастотный импульсный источник питания, твердотельное реле
◆Компоненты автомобильной электроники, аэрокосмической и военной электроники
◆Модуль солнечной панели ; Телекоммуникационный частный обмен, приемная система; Лазерная и другая промышленная электроника
Применение керамической подложки в полупроводниках третьего поколения
Основные силовые устройства, представленные MOSFET, IGBT и транзисторами, занимают место в своих собственных сегментах частот и источников питания. Благодаря всесторонним превосходным характеристикам IGBT, он заменил GTR, став инвертором, ИБП, преобразователем частоты, электроприводом, мощным импульсным источником питания, особенно в настоящее время популярным электромобилем, высокоскоростным железнодорожным транспортом и другими силовыми электронными устройствами в основных устройствах.
Применение глиноземной керамической подложки в области электронной энергетики
В области силовой электроники, такой как импульсный источник питания, электропривод и т.д., диэлектрическая керамическая подложка необходима для достижения лучшей теплопроводности, предотвращения перегорания тока и короткого замыкания.
Применение глиноземокерамической пластины совместного обжига в производстве литиевых аккумуляторов
Руководствуясь рекомендациями искусственного интеллекта и защиты окружающей среды, автомобильная промышленность также запустила электромобили, главным образом за счет аккумуляторных батарей. Литиевые батареи, изготовленные на керамической подложке, могут обеспечивать лучшие функции рассеивания тока и тепла, повышая рыночный спрос на новые энергетические транспортные средства.
2. Преимущества керамической подложки
A. Коэффициент теплового расширения керамической подложки близок к коэффициенту теплового расширения кремниевого чипа, что позволяет экономить Мо листа переходного слоя, экономить трудозатраты, экономить материал и снижать стоимость;
B. Уменьшите сварочный слой, уменьшите термическое сопротивление, уменьшите полость;
C. При том же потоке нагрузки ширина провода из медной фольги толщиной 0,3 мм составляет всего 10% от ширины обычной печатной платы;
D. Превосходная теплопроводность, благодаря чему упаковка чипов получается очень компактной, что значительно увеличивает плотность мощности, повышает надежность системы и устройства;
E. Ультратонкая (0,25 мм) керамическая подложка может заменить BeO без проблем с токсичностью для окружающей среды;
F. Большая грузоподъемность, ток 100А непрерывно проходит через медный корпус шириной 1 мм и толщиной 0,3 мм, повышение температуры составляет около 17 ℃; При токе 100А, непрерывно проходящем через медный корпус шириной 2 мм и толщиной 0,3 мм, повышение температуры составляет всего около 5 ℃.
G. Низкое тепловое сопротивление, термостойкость керамической подложки размером 10×10 мм при толщине керамической подложки 0,63 мм составляет 0,31 К/Вт, толщина керамической подложки 0,38 мм составляет 0,19 К/Вт, толщина керамической подложки 0,25 мм составляет 0,14 К/Вт.
H. Высокая изоляция и устойчивость к высокому давлению для обеспечения личной безопасности и защиты оборудования.
I. Могут быть реализованы новые методы упаковки и сборки, позволяющие получить высокоинтегрированный продукт и уменьшить его размер.
3. Технология керамической подложки
В настоящее время распространенными типами керамических тепловыделяющих подложек являются HTCC, LTCC, DBC и DPC. DBC и DPC для отечественного производства в последние годы стали зрелыми, а производство энергии по профессиональной технологии, DBC - это использование высокотемпературного нагрева Al2O3 и комбинации пластин Cu, его техническим узким местом является нелегкое решение проблемы микропор между Al2O3 и пластиной Cu, что делает массовое производство энергии и выход продукта за счет более сложной задачи. Технология DPC - это использование технологии прямого меднения, осаждения Cu на подложку Al2O3, ее процесс в сочетании с технологией материала и пленки, ее продукт является наиболее часто используемой керамической охлаждающей подложкой в последние годы. Однако его требования к контролю материалов и способности к интеграции технологических процессов высоки, что делает технический порог вхождения в индустрию ЦОД и стабильного производства относительно высоким.
(1) HTCC (Высокотемпературная керамика совместного обжига)
Производственный процесс HTCC очень похож на процесс LTCC. Основное отличие заключается в том, что керамический порошок HTCC не добавляется к стеклянному материалу. Следовательно, керамический порошок HTCC должен быть высушен и отвержден до эмбриональной формы при высокой температуре 1300 ~ 1600 ℃. Из-за высокой температуры совместного обжига выбор материалов для металлических проводников ограничен, основными материалами для него являются вольфрам, молибден, марганец с высокой температурой плавления, но низкой электропроводностью... Например, металл и, наконец, слоистое спекающееся формование.
(2) LTCC (Низкотемпературная керамика совместного обжига)
LTCC также известен как многослойная керамическая подложка совместного обжига при низких температурах. В этой технологии порошок неорганического оксида алюминия и примерно 30-50% стеклянного материала смешиваются с органическим связующим для равномерного смешивания с буровой суспензией. Затем суспензию соскабливают скребком на листы, а затем в процессе сушки из листовой суспензии формуют тонкий кусок необработанной заготовки. Как передача сигналов на всех уровнях
Для внутренних линий LTCC используется технология трафаретной печати для заполнения отверстий и линий печати на необработанных эмбрионах, а внутренние и внешние электроды могут быть использованы соответственно из серебра, меди, золота и других металлов. Наконец, слои укладываются друг на друга и спекаются в печи для спекания при температуре 850 ~900℃.
(3) Медь с прямым соединением (DBC)
Технология прямого нанесения медного покрытия заключается в использовании меднокислородной эвтектической жидкости непосредственно на керамическое покрытие, основной принцип заключается во введении соответствующего количества кислорода между медью и керамикой до или во время процесса нанесения покрытия, в диапазоне 1065 ℃ ~ 1083 ℃, медь и кислород образуют эвтектическую жидкость Cu-O, Технология DBC использует эвтектический раствор для химической реакции с керамической подложкой с образованием фазы CuAlO2 или CuAl2O4, с одной стороны, и для проникновения в медную фольгу, чтобы реализовать комбинацию керамической подложки и медной пластины, с другой стороны.
(4) ЦОД (медь с прямой пластиной)
ЦОД также известен как подложка с прямым медным покрытием. Возьмем в качестве примера процесс изготовления подложки DPC: Прежде всего, керамическая подложка предварительно обрабатывается и очищается, а керамическая подложка напыляется на керамическую подложку и соединяется со слоем медного композита с использованием технологии вакуумного нанесения тонкопленочного покрытия. Затем схема создается с помощью процесса повторной экспозиции, проявки, травления и удаления пленки с помощью фоторезистентности к микротеням желтого света. Наконец, толщина контура увеличивается путем нанесения гальванического покрытия/безэлектродного напыления, и металлизированный контур изготавливается после удаления фоторезистентности.
3. Процесс производства керамической подложки
1. Сверление
Керамическая подложка обычно используется для лазерной штамповки, по сравнению с традиционной технологией штамповки, технология лазерной штамповки обладает преимуществами высокой точности, высокой скорости, высокой эффективности, крупномасштабной массовой штамповки, подходит для подавляющего большинства твердых и мягких материалов, без потерь для инструментов, в соответствии с печатной схемой плата с высокой плотностью межсоединений, тонкая разработка.
Благодаря процессу лазерного сверления керамическая подложка обладает высокой силой сцепления керамики и металла, не отваливается, явление вспенивания позволяет достичь эффекта совместного роста, высокой гладкости поверхности, шероховатости в 0,1 мкм ~ 0,3 мкм, апертура лазерного сверления в 0,15 мм-0,5 мм, даже может достигать 0,06 мм.
2, Покрытый медью
Медное покрытие относится к области без проводов на печатной плате, покрытой медной фольгой, соединенной с проводом заземления, чтобы увеличить площадь провода заземления, уменьшить площадь контура, уменьшить падение напряжения, повысить энергоэффективность и помехозащищенность. Медное покрытие может не только снизить сопротивление заземления, но и уменьшить площадь поперечного сечения контура и усилить зеркальный контур сигнала. Таким образом, процесс нанесения медного покрытия играет очень ключевую роль в процессе изготовления печатной платы на керамической подложке, неполный, усеченный зеркальный контур или неправильное расположение слоя меди часто приводят к новым помехам, негативно сказываются на использовании платы.
3. Травление
Керамические подложки также необходимо протравить, предварительно покрыв рисунок схемы слоем свинцово-оловянного резиста, а затем химически вытравить незащищенную непроводящую медь, чтобы сформировать схему. Травление делится на травление внутреннего слоя и травление наружного слоя, травление внутреннего слоя с использованием кислотного травления, с использованием влажной пленки или сухой пленки в качестве коррозионной стойкости; Внешнее травление - щелочное травление с оловом и свинцом в качестве резиста.
На заводе по производству печатных плат существует множество видов производственного процесса керамических изделий. Говорят, что существует более 30 видов производственных процессов, таких как сухое прессование, затирка швов, экструзия, инжекция, литье под давлением и изостатическое прессование. Поскольку электронная керамическая подложка относится к "плоскому" типу, форма не является сложной, производственный процесс сухого формования и обработки прост, а стоимость низкая, поэтому большинство из них используют метод сухого прессования. Процесс производства электронной керамики для печатных плат сухого прессования в основном включает в себя формование заготовки, спекание заготовки и финишную обработку, формирование схемы на подложке.
1. Экологически чистое производство керамической подложки (формовка)
Используйте порошок оксида алюминия высокой чистоты (содержание ≥95% Al2O3) (в зависимости от назначения и способа изготовления требуются различные размеры частиц). Например, от нескольких неграмотных до десятков микрон) и добавки (в основном клеи, диспергаторы и т.д.). Образуют "пасту" или обработанный материал.
(1) Сухое прессование керамической основы для получения зеленых деталей (или "зеленки").
В заготовке для сухого прессования используется глинозем высокой чистоты (электронная керамика с содержанием глинозема более 92%, в большинстве случаев используется 99%), порошок (частицы сухого прессования не должны превышать 60 мкм, для экструзии, прокатки, инжекции и других видов порошковых частиц следует контролировать в пределах 1 мкм), добавьте соответствующее количество пластификатор и связующее, равномерно перемешанные после сухого прессования заготовки. В настоящее время толщина квадратных или круглых заготовок может достигать 0,50 мм или даже ≤0,3 мм (в зависимости от размера пластины). Заготовки сухого прессования могут быть обработаны перед спеканием, например, для определения размеров и сверления. Подвергайте механической обработке, но будьте осторожны, чтобы компенсировать усадку по размеру, вызванную спеканием (увеличьте величину усадки).
(2) Получение зеленой заготовки методом намазывания керамической подложки.
Жидкий клей (порошок оксида алюминия + растворитель + диспергатор + клей + пластификатор, равномерно перемешанный + просеивание) производство + литье поточным способом (в машине для литья поточным способом наносится клей на металлическую или термостойкую полиэфирную ленту) + сушка + обрезка (также может быть другая обработка) + обезжиривание + спекание и другие процессы. Он может реализовать автоматизацию и масштабирование производства.
2. Спекание и финишная обработка зеленой заготовки после спекания. Необработанные части керамической подложки часто нуждаются в "спекании" и отделке после спекания.
(1) Спекание необработанной керамической подложки.
"Спекание" керамической заготовки относится к процессу "спекания" заготовки (объема) в полости, воздуха, примесей и органических веществ, таких как удаление сухого давления, с целью ее улетучивания, сжигания, экструзии и удаления частиц оксида алюминия. Добейтесь тесного контакта или комбинированного процесса выращивания, поэтому после спекания керамической заготовки произойдет потеря веса, усадка по размеру, деформация формы, увеличение прочности при сжатии, уменьшение пористости и другие изменения.
Методы спекания керамической заготовки следующие: ① атмосферное спекание, спекание без давления приведет к большой деформации; ② спекание под давлением (горячее прессование), спекание под давлением, позволяет получить хорошие плоские изделия, является наиболее часто используемым методом; ③ Горячее изостатическое спекание - это использование спекания горячим газом под высоким давлением. Характерные для него изделия изготавливаются при одинаковой температуре и давлении. Все виды производительности сбалансированы, стоимость относительно высока. В добавленной стоимости изделий аэрокосмической промышленности, национальной обороны и военной продукции при использовании этого метода спекания, таких как зеркала военного назначения, ядерное топливо, бочонки и другие изделия. Температура спекания сырых заготовок из глинозема сухого прессования в основном составляет от 1200℃ до 1600℃ (в зависимости от состава и флюса).
(2) Финишная обработка керамической основы после спекания (варки) заготовки.
Большинство спеченных керамических заготовок требуют финишной обработки. Цель состоит в том, чтобы: ① получить ровную поверхность. В процессе высокотемпературного спекания сырой заготовки из-за дисбаланса распределения частиц, пустот, примесей и органических веществ в сырой заготовке это приведет к деформации, неравномерности или чрезмерной шероховатости и перепаду температур. Эти дефекты могут быть устранены путем финишной обработки поверхности; ② Получите поверхность высокого качества, такую как зеркальное отражение, или улучшите смазывающую способность (износостойкость).
Обработка поверхности полировкой заключается в использовании полировальных материалов (таких как карбид кремния, B4C) или алмазно-песчаной пасты для постепенной полировки поверхности от грубого абразива к мелкому. Вообще говоря, для достижения этого требуется использование порошка AlO или алмазной пасты толщиной ≤1 мкм, а также лазерная или ультразвуковая обработка.
(3) прочная (стальная) обработка.
После полировки поверхности, чтобы улучшить механическую прочность (например, прочность на изгиб и т.д.), вакуумное покрытие электронным лучом, вакуумное напыление, испарение химического пара и другие методы могут быть использованы для нанесения слоя пленки из кремниевого компаунда, термообработка при температуре 1200 ℃ ~ 1600 ℃ может значительно улучшить механическая прочность керамических деталей!
3. Сформируйте проводящий рисунок (схему) на подложке
Для обработки проводящей графики (схем) на керамических подложках необходимо сначала изготовить керамические подложки с медным покрытием, а затем изготовить керамические печатные платы в соответствии с технологией печатных плат.
(1) Формирование керамической подложки, покрытой медью. В настоящее время существует два способа формирования керамических подложек с медным покрытием.
① Способ ламинирования. Он формируется путем горячего прессования одной стороны окисленной медной фольги и глиноземной керамической подложки. То есть керамическую поверхность обрабатывают (например, лазером, плазмой и т.д.), получают активированную или шероховатую поверхность, а затем в соответствии с "медная фольга + термостойкий связующий слой + керамика + термостойкий связующий слой + медная фольга" ламинируют вместе, после 1020 ℃ ~ 1060 ℃ спекание, образование двухстороннего керамического ламината с медным покрытием. ② Способ нанесения гальванических покрытий. После плазменной обработки керамическая подложка представляет собой "напыленную титановую пленку + напыленную никелевую пленку + напыленную медную пленку", а затем обычное гальваническое покрытие меди до требуемой толщины меди, то есть формирование двухсторонней керамической подложки с медным покрытием.
(2) Изготовление односторонних и двухсторонних керамических печатных плат. В соответствии с традиционными технологиями изготовления печатных плат используются керамические подложки с односторонним и двусторонним медным покрытием.
(3) изготовление многослойных керамических пластин.
① В одинарных и двойных панелях многократно наносится слой изоляции (оксид алюминия), спекание, разводка проводов, спекание для формирования многослойной печатной платы или использование технологии литья для завершения. ② Керамическая многослойная пластина изготавливается методом литья. Необработанную ленту формуют на литейной машине, затем сверлят, закупоривают (токопроводящий клей и т.д.), печатают (токопроводящая схема и т.д.), режут, ламинируют, изостатически прессуют для формирования многослойной керамической пластины. Компания Hitech Circuits имеет более чем 10-летний опыт производства керамических подложек, поэтому не стесняйтесь обращаться к ним, если вам нужно узнать больше по техническим вопросам.
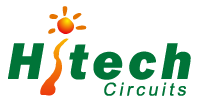
+86-755-29970700 or +86-(0)181 2646 0264
sales@hitechpcb.com; sales18@hitechcircuits.com
2F, Building C, Suojia Technology Park, Hangcheng, Bao’an, Shenzhen, Guangdong, China 518126